① Improved production line operation reliability
1. The main process tanks are all equipped with spare tanks to facilitate slag liquid cleaning in the tank and adjust process parameters at any time, which increases the overall operation stability of the production line.
2. The wire rod hook lifter adopts domestic first-class universal lifting equipment for vertical lifting. The product is mature, safe and reliable, and easy to maintain. The manipulator adopts multiple sets of steering wheels, guide wheels and universal steering gear to prevent swaying of the moving vehicle. At the same time, it cooperates with precision-machined tracks (optional), which eliminates the wear of the main track and improves the life of the ring track.
3. Improved wire rod hook protection. The original hook was only used for anti-corrosion treatment and FRP was applied. In actual use, it was found that the wire rod and the anti-corrosion layer were in hard contact due to the lifting and running links, which caused the anti-corrosion layer to crack and reduce the use time. When the hook is made this time, the contact surface is covered with a layer of PPE material to slow down the collision and protect the anti-corrosion layer, which greatly prolongs the use time.
4. The design of the online slag removal system ensures that the production line can process the phosphorus slag online without stopping production. At the same time, the inner wall of the phosphating tank and the heater are fully covered with expensive polytetrafluoroethylene (optional), which greatly increases the cleaning cycle of the tank and is easier to clean, greatly reducing the operating intensity and difficulty of the workers, and the phosphating turbid liquid. After filtering, it can be used again, saving production and running costs.
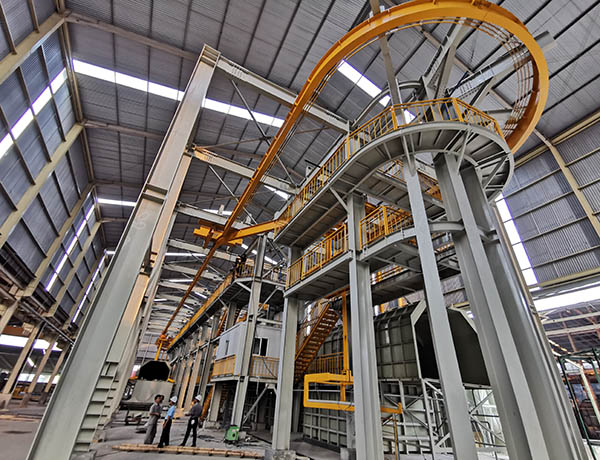
② the degree of automation of the production line has been further improved
1. In addition to the addition and subtraction of high-level tanks in each pickling tank, bypass pipes and acid pumps are newly added in this design, which can be flexibly operated according to process parameters.
2. This production line is newly equipped with electric flat cars for loading and unloading rails, which are operated by control computer instructions, reducing supporting equipment, reducing labor costs and maintenance costs.
3. An automatic metering and feeding system (optional) is added to the phosphating tank. Multi-point spraying is used to add liquid evenly and the degree of automation is high.
4. Industrial computer control, perfect, clear and friendly man-machine interface, multiple dynamic real-time screens, presenting the operating status and operating parameters in the production line in front of the control personnel, switching freely, and intuitive operation.
5. The adopted Ethernet wireless transmission operation scheme is the leading in China. The online random process time is adjusted to the millisecond-level operating parameters and the control of the mobile car program, without the need to verify and change the site one by one. The system runs stably and has a high degree of automation.
6. Improved sensor design and automatic collision avoidance procedure for robot
Due to design defects, robots in traditional production lines often cause collisions between vehicles, which not only disrupts process parameters, but also affects the normal operation of the production line and increases maintenance costs.
After the upgrade, the hardware uses laser positioning, two-way sensors combined with photoelectric coding, and multiple positioning, which perfectly guarantees that the design process corresponds to the actual slot one-to-one to prevent misalignment. In the process, the collision avoidance program has also been improved, changing the hardware control to software + hardware control, logical collision avoidance, and the effect is obvious, preventing major equipment accidents.
Post time: Aug-23-2022